Завод «Микрон»: сердце российского хайтека
На модерации
Отложенный
Ругать отечество стало модным ещё со времён распада СССР. Больше всего достаётся высокотехнологичной отрасли: дескать, мы безнадёжно отстали и катимся в каменный век. Однако мало кто знает, что в нашей стране есть предприятия, оказывающие заметное влияние не только на отечественный, но и на весь мировой рынок. С одним из них, зеленоградским заводом «Микрон», мы и познакомим вас в этом репортаже.
Расположен завод на окраине Зеленограда, на самой границе городской цивилизации. Всего в километре от него, вдаль от Москвы по Ленинградскому шоссе, находится дачный посёлок Искра, а следом за ним — коттеджный комплекс «Лисичкин лес». На этот самый лес, окружающий загородные участки и вплотную примыкающий к городу, открывается роскошный вид прямо из окна основного здания предприятия. Высокая 17-этажная «башня» является единственным высотным зданием в округе, возвышаясь над соседними двух-трёхэтажными строениями, словно капитанская рубка
Вид из окна главного административного здания («Лисичкин лес»)
По сути, так оно и есть: там сосредоточен управленческий персонал и научные кадры, в то время как производство осуществляется в обширных невысоких цехах на остальной территории завода, расположенной по другую сторону дороги. Чтобы попасть туда, нужно воспользоваться подземным переходом, вход в который возможен только из этого здания — словно в голливудском блокбастере о научной мега-корпорации, ведущей секретные разработки. Сходство ещё больше усиливается, когда на пропускном пункте приходится подписывать бумагу о неразглашении конфиденциальной информации. Другое обязательное требование — надеть на обувь бахилы. Полупроводниковое производство требует соблюдения чистоты, или, как тут говорят, «гигиены производства», прямо с порога. И наконец, мы можем войти внутрь, быть может, самого современного производства на территории России.
Возрождение из пепла
Завод «Микрон» был создан в 1964 г. для разработки и промышленного производства отечественных интегральных микросхем. Пробыв 20 лет в статусе госпредприятия, с приходом 90-х он на себе испытал все «прелести» перестройки: ежегодное сокращение госфинансирования, устаревание оборудования, потерю квалифицированных кадров. Ребром встал вопрос о сохранении его как компании-производителя, либо превращения в банальный набор арендуемых помещений. Основная проблема была в том, что продукция как самого зеленоградского завода, так и остальных предприятий электронной промышленности, перестала пользоваться спросом: российская электронная бытовая техника не пользовалась популярностью, проигрывая конкуренцию хлынувшим в нашу страну зарубежным изделиям, как по эксплуатационным параметрам, так и по цене. Тем не менее, руководством было принято непростое решение о сохранении производства и его развитии. Непростым оно было потому, что требовало от оставшихся сотрудников большого напряжения сил, в то время как сдавая помещения в аренду и потихоньку распродавая оставшееся оборудование, можно было спокойно просуществовать ещё лет десять.
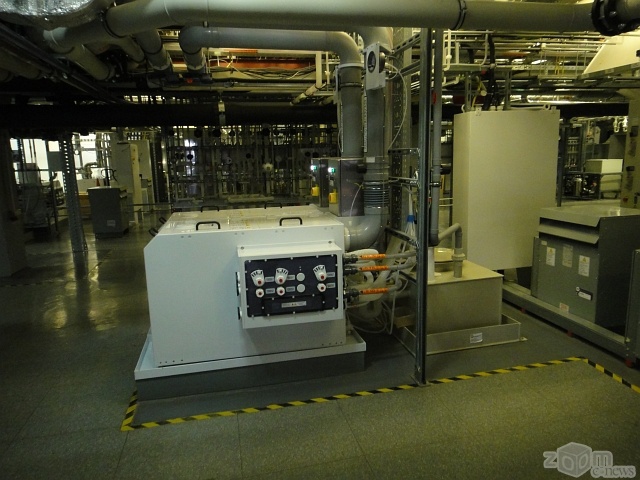
Оборудование на техническом этаже
Основной вопрос, требовавший незамедлительного решения, — поиск рынка сбыта. О равной конкуренции с крупнейшими производителями из Юго-Восточной Азии и речи не было — объём стартовых вложений, необходимых для этого, превышал все мыслимые возможности. Но вдруг как нельзя кстати подвернулись наши сотовые операторы: в связи с лавинообразным ростом абонентской базы им требовалось большое количество новых сим-карт, и поэтому первый шаг решено было сделать именно в этом направлении. Несмотря на кажущуюся бесперспективность, сим-карта — хороший продукт для развития полупроводникового производства. Во-первых, технология отлажена, во-вторых, не требуется дорогостоящего оборудования, и самое главное — их нужно много! Совместно с крупнейшей мировой компанией-производителем смарт-карт Giesecke&Devrient в 2006 году было создано производство SIM-карт: закуплено необходимое оборудование и освоена технология производства, пока ещё на импортных чипах. Этот проект позволил «Микрону» найти средства на освоение технологии производства микросхем по топологии 180 нм.
Немного о технологиях
Здесь нам придётся сделать небольшое отступление, чтобы развенчать два мифа о технологиях изготовления чипов, бытующих в околокомпьютерной среде. Миф первый: «180 нм — это вчерашний день, нам нужно осваивать 22 нм, как это делает Intel, а ещё лучше сразу 10 нм, с „заделом“ на будущее». На самом деле, использование таких литографических норм требуется только для некоторых узкоспециализированных применений: центральные и графические процессоры, «системы-на-кристалле» (SoC), и, возможно, очень крупные программируемые вентильные матрицы (FPGA). В остальных случаях это совершенно не оправдано: «тонкий» техпроцесс более дорогой, что увеличит себестоимость изделия, а также имеет более низкий процент выхода годных чипов, что только удорожает продукт. Никаких преимуществ перед микросхемами, сделанными по более «грубому» нормативу, та же сим-карта иметь не будет — быстродействие ей увеличивать незачем, а некоторое возможное уменьшение потребляемой мощности будет настолько незначительно по сравнению с остальными узлами телефонного аппарата, что едва ли сможет увеличить время его автономной работы хотя бы на пару минут.
Оборудование «чистой комнаты»
Второй миф — что же представляет собой процесс «закупки технологии». Наверное, многие представляют себе его наподобие покупки кухонного гарнитура: выбрал дизайн мебели, подобрал к ней бытовую технику, заплатил деньги — и дело в шляпе: приехали бравые молодцы, собрали оборудование, подключили, и можно пользоваться! Однако в мире высоких технологий всё гораздо сложнее. Во-первых, нанометр нанометру рознь. Пожалуй, это будет третьим развенчиваемым мифом. Каждая фирма, обладающая определённой технологией, реализует её по-своему. 180 нм от Siemens будет совсем не то, что 180 нм от Global Foundries. Там будет использовано разное оборудование, да и стадии изготовления продукции (и даже их количество!) будут сильно отличаться. Так вот, покупка технологии означает, что вам продают «ноу-хау» — знание о том, что следует делать для получения готового продукта. А всё остальное, начиная с приобретения оборудования, и вплоть до набора библиотек для проектирования топологии, приходится создавать самому. Можно провести аналогию с известным ПО Adobe Photoshop: пусть лицензию на программу вы купили, но устанавливать её и тем более рисовать в ней за вас никто не будет. Более того, в редакторе нет ни одного плагина — создавать их вам тоже придётся самостоятельно.
Адаптеры питания как двигатель прогресса
Самостоятельно «перепрыгнуть» через несколько технологических поколений было невозможно, поэтому ставка была сделана на лицензирование технологии производства микросхем. Зеленоградское предприятие на тот момент искало технологии, которые позволят освоить производство чипов не только для SIM-карт, но и для электронных документов, транспортных билетов, социальных карт. Были тщательно изучены два бизнес-плана, предложенные крупными европейскими производителями чипов: Infineon Technologies AG и STMicroelectronics. Infineon предлагал технологию 250 нм, STMicroelectronics — 180 нм. Выбор в итоге пал на STM, несмотря на то, что для реализации их технологии требовалось закупить более дорогостоящее оборудование. Всего «Микрон» заключил тогда соглашения с 42 поставщиками из 10 стран мира: в число поставщиков оборудования вошли M+W Zander, Air Liquid, Hager+Elsasser, Applied Materials, ASML и многие другие. Весь проект обошелся в 230 млн. долларов. Чтобы привлечь необходимые средства, была использована процедура IPO. В 2007 году на «Микроне» был налажен выпуск кристаллов для сим-карт на пластинах диаметром 200 мм, а упаковку в пластик уже производили фактически в соседнем цехе. Сейчас предприятие готовится выпускать для операторов связи совершенно новый тип SIM-карт — с электронной цифровой подписью.
Контроль давления в трубопроводе
Другой крупный рынок сбыта, на котором присутствует «Микрон», представляют собой блоки питания. Нет, не такие мощные и относительно сложные, как установлены в персональных компьютерах, а те, что и блоками питания не считают, презрительно называя «адаптерами». Их мощность — единицы или десятки ватт, а цена составляет несколько долларов. Тем не менее, внутри каждого из них есть микросхема, управляющая его работой и регулировкой напряжения. Маленькая и простая, стоимость которой всего несколько центов. Но учитывая сколько таких адаптеров повсеместно выпускают во всём мире, количество этих микросхем просто астрономическое. И кристалл производства «Микрон» стоит примерно в каждом пятом адаптере! Но не спешите разламывать первый попавшийся адаптер, оказавшийся под рукой, в поисках заветного логотипа внутри. Большая часть чипов продаётся с завода по оптовым поставкам, причём без корпусов — на пластинах, ибо так дешевле. А где-нибудь в Китае их установят в корпуса, на которых будет написано «Burr Brown» или «Hangzhou Silan Microelectronics». И только распилив пластик, при помощи сильной лупы можно увидеть внутри на кристалле заветный символ «Микрона». И, к сожалению, никаких слоганов на корпусе изделия, наподобие «Intel Inside».
Измерительное оборудование в чистой комнате
По мере того, как производство продолжало развиваться, заказчиков у «Микрона» прибавлялось. Следующий крупный прорыв случился благодаря билетам метро. Как известно, внутри них тоже есть крохотный чип и проволочная антенна. Воспользовавшись услугами отечественного производителя, наладившего выпуск электронных билетов, Московский Метрополитен смог избавиться от подделок жетонов, а завод получил хорошего заказчика. Уникальность предложения завода в том, что все части билета: чип, инлей (пластиковая подложка с антенной) и внешняя картонная оболочка изготавливаются в одном месте, избавляя Метрополитен от необходимости искать все элементы билета у разных поставщиков и координировать их производство.
Как делают чипы
Наверное, у многих слова «полупроводниковое производство» вызывают в памяти рекламные фотографии Intel, изображающие человека в защитном костюме в виде скафандра, держащего в руках кремниевую пластину. Отчасти этот образ преувеличен: такая чистота воздуха в «чистой комнате» в современном производстве не требуется, так как все критичные к пыли операции выполняются автоматически внутри изолированного от внешней среды оборудования, а пластины находятся в герметичных пластиковых контейнерах. Тем не менее, спецодежда у сотрудников всё же имеется, однако она не закрывает лицо полностью, скорее напоминая противомоскитный комбинезон, в котором можно свободно дышать, но через «медицинскую маску». Смысл её наличия в том, чтобы уменьшить количество пыли до уровня, с которым легко справляются входные фильтры. А вот к чистоте внутри гермобоксов требования, наоборот, возросли, так как с уменьшением норм техпроцесса пластины становятся всё более «нежными».
Пластины с кристаллами «Эльбрус»
Всё оборудование достаточно компактное и напоминает стоящие там и сям холодильники или шкафы, с сопутствующими компьютерами на столах, словно в обычной IT-организации. Но это лишь верхушка айсберга: объём инфраструктуры производства, обеспечивающей его бесперебойную работу, поистине поражает! Под цехами скрывается огромный технический этаж, где установлены насосы, ёмкости, фильтры, источники питания, и прочее оборудование. Основное «сырьё» для производства вовсе не кремний, которого требуется всего лишь единицы килограмм, а сверхчистая вода — промывки в ней происходят почти на всех этапах производственного процесса. Причём вода должна быть не просто с отсутствием примесей, в ней не должно быть даже ионизированных молекул. Степень чистоты деионизированной воды должна составлять не более 1−2 ppb, или миллиардных долей (ppb — «parts per billion»). Чтобы получить такую воду, требуются специальные фильтры стоимостью несколько миллионов рублей, менять которые необходимо каждые три месяца. А для хранения и подачи нужны особые ёмкости, не выделяющие примесей в воду. Вплоть до того, что сварка металлических труб в аргонной среде ведётся с подачей сверхчистого аргона, иначе примеси в нём загрязнят сварной шов, частицы которого попадут и в воду. Промывать некачественный трубопровод бесполезно — пройдут века, прежде чем количество примесей уменьшится до приемлемого уровня. Единственный выход — полностью заменить его.
.
Пластина с чипами RFID 180 нм (выставочный образец)
Помимо сверхчистой воды, на некоторых стадиях техпроцесса необходимо использовать различные газы и жидкости, большая часть из которых ядовиты или агрессивны. Изопропиловый спирт, пероксид водорода, соляная, серная, и фтороводородная кислота, аммиак, фторметан, закись азота — вот делеко не полный перечень химических реагентов. Утечки на таком производстве могут представлять серьёзную опасность для здоровья персонала, поэтому технические этажи содержат аварийные комплекты химической и газовой защиты: противогазы и кислотостойкие комбинезоны.
В обязательном порядке оборудованы места оказания экстренной медицинской помощи, например, душевая стойка для смывания попавших на кожу веществ с двумя отдельными форсунками для промывки глаз, для подачи воды в которую достаточно сорвать подвешенный на уровне груди проволочный рычаг. Другие средства соблюдения безопасности — двойные трубопроводы, где каждая основная магистраль с реагентом окружена второй, защитной трубой, а также обязательные таблички на каждом вентиле, показывающие положение, в котором ему следует находиться (открытом или закрытом); при повороте вентиля табличка меняется. И хотя за всё время существования завода аварий на технических этажах не было, при их посещении мы невольно ощущали спиной лёгкий холодок.
Лента со СМАРТ-картами (выставочный образец)
Несложно догадаться, что поддержание всего оборудования в рабочем состоянии требует серьёзных затрат. Причём их сумма практически не зависит от того, идёт ли на производстве выпуск продукции, или оно простаивает. Отключение всех систем и последующий повторный запуск настолько трудозатратны и дороги, что выгоднее месяцами поддерживать холостую работу системы, чем останавливать её и запускать снова. Что же касается максимальных возможностей производства, то они составляют десятки миллионов кристаллов ежемесячно, что в разы превосходит фактическую загрузку. Поэтому поиск заказов и рациональное использование имеющихся мощностей — самая актуальная задача для руководства завода.
И вот они, процессоры!
В 2012 году наше государство снова обратило внимание на возможности завода. Заключив партнёрство с корпорацией РОСНАНО, удалось закупить технологию и оборудование для выпуска продукции по топологии 90 нм с медной металлизацией у той же компании STMicroelectronics. Это оказалось как нельзя кстати, так как действующей линии 180 нм уже стало не хватать для удовлетворения возросших требований ряда заказчиков. Текущие возможности завода на топологиях 180−90 нм сегодня составляют 36 тысяч 200-миллиметровых пластин в год. Благоприятной возможностью освоить выпуск своей продукции в России воспользовалась компания МЦСТ, передавшая на «Микрон» производство первого отечественного 90-нм микропроцессора «Эльбрус-2С», о котором мы уже писали. Правда, для этого им пришлось совместно со специалистами «Микрона» переработать всю технологическую цепочку, изначально ориентированную на тайваньского производителя, но эта сложная задача была успешно решена
Электронные билеты (выставочный образец)
На новой производственной линии выпускаются кристаллы оперативной памяти 32 и 16 Мбит и заказные чип-контроллеры. Различные государственные программы также подразумевают использование мощностей зеленоградского предприятия: создание биометрических паспортов, выпуск универсальных электронных карт — ещё один рынок сбыта продукции. В перспективе маячит участие в создании отечественной платёжной банковской системы и электронного документа гражданина: там могут использоваться чипы и пластиковые карты производства «Микрона».
ОЗУ 4 Мбита в радиационно-стойком исполнении (выставочный образец)
А уже в 2013 году специалисты предприятия самостоятельно смогли переработать технологию 90 нм для выпуска продукции по нормам 65 нм. Это ещё больше расширяет возможности завода, позволяя, в частности, наладить выпуск следующего поколения процессора «Эльбрус» — «Эльбрус-4С». Разработаны также другие уникальные технологии, например, сочетание кремния и германия, арсенид галлия или кремний на изоляторе — радиационно-стойкое исполнение чипов.
В ожидании светлого будущего
Итак, раз подавляющее большинство задач уже решены, можно ли успокоиться? Можно было бы закончить репортаж на этой радостной ноте, но в видении будущего не всё так радужно. «Открытый рынок», за который мы все так ратовали, оказался не так уж хорош для микроэлектронного завода. Сегодня «Микрон» со своими чипами на отечественном рынке вынужден конкурировать с иностранными производителями аналогичной продукции без какой-либо поддержки со стороны государства. А ведь те «самые тонкие нанометры», которые почти никому не нужны, на самом деле, имеют прямое влияние на престиж страны, её место в рейтинге высокотехнологихных государств. Занять место лидера более почётно, чем постоянно «догонять и перегонять». Однако никакому отдельно взятому предприятию, даже такому крупному, как «Микрон», в одиночку не осилить столь глобальную цель. Ежегодный бюджет, выделяемый компанией Интел на разработки, составляет уже более 10 млрд. долларов. Может ли о таком мечтать отечественная хай-тек компания?
Литографический фотошаблон 180 нм (выставочный образец)
За рубежом для развития высоких технологий компании могут взять кредит под 3% годовых сроком на 20 лет, и на 5 лет освобождаются от уплаты всех налогов, а у нас вынуждены сражаться за место под солнцем «на общих основаниях». Финансовая поддержка государства есть, но возможна лишь в обмен на акции, что, по понятным причинам, не устраивает ни основных акционеров, ни руководство компании. Свободную экономическую зону на территории завода создать пока тоже не удаётся. А это бы очень помогло снизить затраты на импорт материалов, компонентов и оборудования, коммунальные платежи — ведь, потребляет завод и воду и электроэнергию в больших объемах и без каких-либо льгот
Цифровой RISC-процессор 180 нм (выставочный образец)
Если сравнить экономические условия, которые создают европейские и азиатские правительства для своего хай-тека, наше пока очень и очень сильно «проигрывает» в этом, хотя публичной риторики о необходимости развития высокотехнологичных производств и импортозамещении — хоть отбавляй
Пластина 200 мм, 90 нм в руке
Однако смещение акцента постепенно происходит в нужном направлении, и если сегодня наши чиновники уже обратили внимание на возможности завода, есть шанс, что завтра они поймут и то, что подобные предприятия следует поддерживать на государственном уровне, начиная с подготовки специалистов и заканчивая ограничением присутствия иностранных производителей на российском микроэлектронном рынке. И наша страна с гордостью сможет войти в группу лидеров научно-технического прогресса. Почему бы и нет?
Автор: Владимир Иванов
Комментарии
Вот сайт о новых производствах в России! http://www.sdelanounas.ru/
Комментарий удален модератором
это правильно, но пока в этом деле мы не конкуренты он туда не полезет...
он лезет туда, где у нас есть независимость и которую нужно уничтожить...
.
Лампы используют в топовых уселителях и оборудовании для электро гитар. В интернете есть об этом.
Не российское, а советское.
.
ОАО «Светлана» более 120 лет и прекрасно себя чувствует.
Выпускает:
полупроводниковых приборов и интегральных схем;
оптоэлектронных и светотехнических приборов;
микроволновых приборов;
рентгеновских трубок всех классов и назначений;
генераторных и модуляторных ламп;
приёмно-усилительных ламп для аудиотехники класса “Hi-Fi”;
технологического оборудования.
Более 20% выпускаемой «Светланой» продукции идет на экспорт.
.
Дочернии компании:
Девять штук разно направлены в своей области.
А еще, отдельно, совмесное производство с другими компаниями в том числе с Хитачи.
.
http://www.svetlanajsc.ru/index.php/ru/
это не важно...
в свое время танки и трактора тоже делали на немецких и американских станках...
- где суть?
- за углом...
а с чего они появятся...
пока стоимость "этого прибора" в "китае" будет меньше собственного производства - никто не будет финансировать это производство...
по этой же причине у нас завозят еду, одежду и т.д.
протекционизмом государства пользуются только особо приближенные, типа автопрома - ваз например
например оружие (стрелковое) можно ввозить только если в штатах производится 30% комплектующих...
хавчик завозить вообще проблема...
даже самим америкосам запрещено выращивать овощи у себя на участке - поддержка фермеров...
МП 26 был... :)
Подземный переход был и раньше, а вот бахил не было.
Комментарий удален модератором
вообще-то вопрос не корректен...
нужно учитывать нашу "покупную способность"... :)
скажем, та же стоимость рабочего часа у нас и у них, мягко говоря разная...
в этом разрезе и все остальное также имеют разные цены...
для примера, Пентагон покупает молотки за 500 долларов
но думаю, что нашим и 1 млрд баксов на разработку не доступен...
автор статьи на все ответил
"За рубежом для развития высоких технологий компании могут взять кредит под 3% годовых сроком на 20 лет, и на 5 лет освобождаются от уплаты всех налогов, а у нас вынуждены сражаться за место под солнцем «на общих основаниях». "
а вот из:
"Первое место по объёму НИОКР занимают США (385,6 млрд; 2,7 % от объема собственного ВВП)
Второе место занимает Китай (153,7 млрд; 1,4 % ВВП)
Третье место принадлежит Японии (144,1 млрд; 3,3 % ВВП)
Россия замыкает десятку мировых лидеров (23,1 млрд; 1 % ВВП)"
это смотря в чем...
если касается военки, космоса и т.д., то основном всё спонсирует государство...
что касается частных компаний в этом направлении, то они делают "пилотный" вариант разработки, достаточный чтобы убедить и вытянуть бабки на дальнейшее из того же бюджета...
по крайней мере так в сша